Five Common Construction Mistakes Avoided by Using an Inspection and Test Plan
construction businesses to establish safety programs to ensure safety and the quality of the project.
Below are five of the common pitfalls that construction businesses face:
1) Failure to identify problem areas early:
Construction work has critical components or difficult parts. Project managers should be able to identify the risks that come along with each task to be performed for the completion of the project. Risks should be identified beforehand to help project managers address them before they occur and lead to costly incidents.
2) Failure to stick with the schedule:
An essential component of a project’s effective completion is scheduling. Without proper scheduling in place, things may get muddled between renting equipment, bringing in subcontractors, ordering supplies, getting permits, and performing required inspections, tests, and surveys.
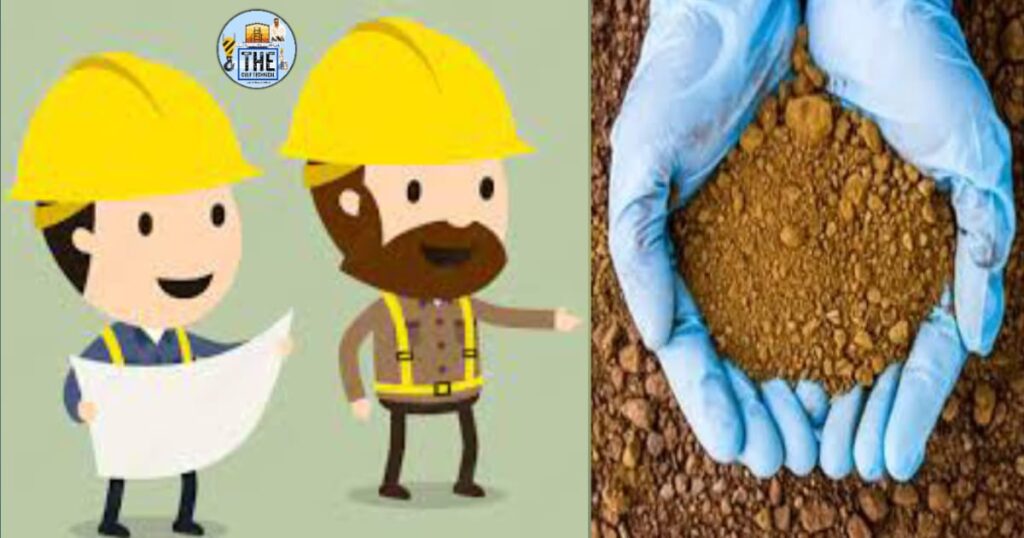
3) Going over the budget:
Project budgets frequently go over for a variety of reasons. Projects mainly go over budget due to these three main reasons:
1) No one is accountable for the budget;
2) the project drags past the deadline; and
3) While some of the other reasons are unanticipated, many of them may actually be anticipated and handled to reduce the amount of overage; the project either falls short of or exceeds the boundaries specified for the scope of the project.
4) Not Securing All Required Construction Permits
Obtaining permits can be a time-consuming process, so it is crucial that the permits required for the project are outlined and determined in advance to avoid delays to the project timeline. Permits guarantee safety and enforce appropriate safety standards that assure protection not only for the client or occupants of the space but also for the workers. It also helps to keep your insurance valid should an injury or accident occur.
5) Inadequate Supervision
Many crucial project steps are often missed because of the sheer volume of work that needs to be done. For example, poor supervision increases the risk of construction defects leading to reworks as well as accidents and injuries. These problems are easily avoided with the presence of a quality system, such as an inspection and test plan. In order to give the construction company and its client a clear and coherent plan for managing inspection and test operations that will provide quality assurance, control, and recorded evidence of produced works, it is best practice to have one developed before beginning the works.