Working Load Limit vs Breaking Strength
The working load limit (WLL), also known as the safe working load (SWL), rated capacity, or working load, is the maximum weight or force that a piece of lifting equipment is intended to handle under normal conditions. The manufacturer typically determines the WLL and places it on the equipment, along with other crucial details like the model number, serial number, and date of manufacture.
Contrarily, breaking strength—also referred to as ultimate strength, tensile strength, or breaking load—is the highest weight or force that a piece of lifting equipment can support before failing; it is typically much higher than the WLL and is ascertained through destructive testing of the equipment.
The safety factor, or factor of safety, is the ratio of the breaking strength to the WLL and indicates the level of safety incorporated into the equipment; the higher the safety factor, the safer the equipment. The typical safety factor for lifting equipment is usually 3:1 or higher, meaning that the breaking strength is at least five times the WLL. This difference between the WLL and breaking strength is significant because it establishes the safety margin, or factor of safety.
Determining the Appropriate Rating
A number of considerations should be taken into account when selecting lifting or rigging equipment, including the angle of the load, the number of attachment points, and the equipment’s condition. The appropriate WLL should be determined based on the intended use and the weight or force that will be applied. The WLL should be equal to or greater than the weight or force being lifted or pulled.
The breaking strength and safety factor must be known in order to calculate the WLL, which is determined by dividing the breaking strength by the safety factor. Thus, if the breaking strength is 10,000 pounds and the safety factor is 5:1, the WLL would be 2,000 pounds.
Commonly Asked Questions
Q: Can the WLL be exceeded?
A: No, the WLL should never be exceeded, as it could cause the equipment to fail and result in injury or damage.
Q: Can the breaking strength be utilized as the WLL?
A: The breaking strength could lead to equipment failure and injury; hence, it should not be utilized as the WLL since it does not provide a safety margin or factor of safety.
What is the safety factor when lifting equipment? The safety factor, also known as the factor of safety (FOS), is a characteristic that we calculate by dividing the structural strength by the minimum structural strength required. The higher the FOS, the less likely it is that the structure will be damaged and the more stress cycles it can withstand.
Thus, the safety factor guarantees safe operations by determining the maximum weight that lifting equipment may safely withstand when in use.
A ratio is used to represent the safety factor. For example, if your equipment needs to lift 2,000 kg and its safety factor is 4:1, it will be designed to lift up to 8,000 kg.
The materials and equipment used determine the safety factor.
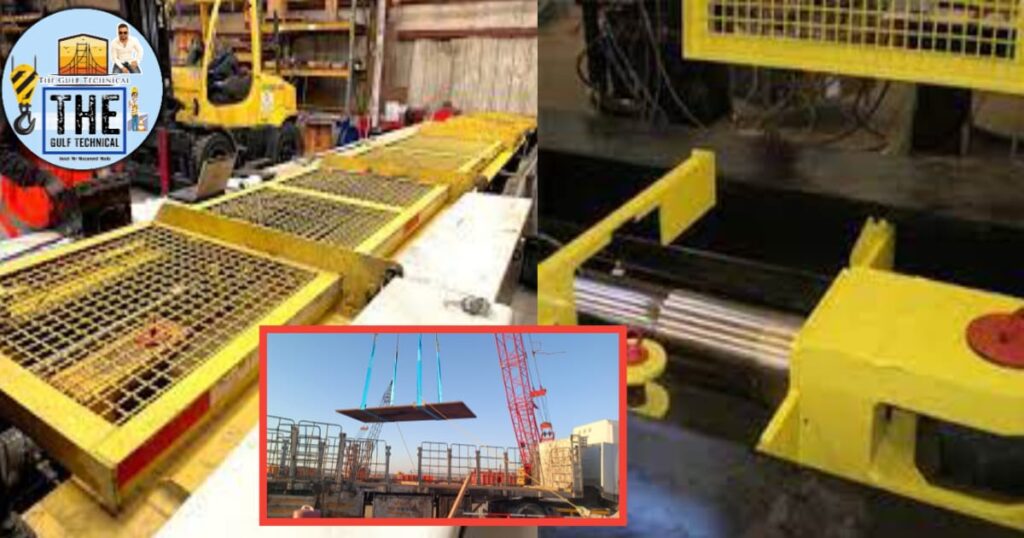
The safety factor in lifting equipment design: To determine safety limitations in any lifting solution, we must compute the forces we apply to the equipment.
Legal standards pertaining to safety factors for lifting equipment put on the market differ globally. Here are a few examples:
It must be between 4:1 and 7:1 for rigging equipment and between 2:1 and 3:1 for hoisting devices in the US and the EU.
When designing lifting equipment, the manufacturer can determine the maximum load that a piece of equipment can safely withstand by either mathematically calculating the equipment’s safety factor or testing the equipment repeatedly until it breaks.
1) ASME
2) BSEN
As per ASME, crane utilization is 85 %
As per BSEN, 75% is right
When making a lifting plan, it should have a contingency factor. 1.2 multiplied by the load To protect percentage
What distinguishes a working load from a breaking load?
Importantly, this information refers to the undamaged, new condition. If the pulley, carabiner, etc. is used on a regular basis, this will affect the breaking load. The minimum breaking load indicates the force at which the material fails. To put it another way, this value shows the minimum force the product must withstand once it breaks, tears, or something similar. The working load indicates the force with which the material may be regularly loaded in everyday work.
A pulley with a breaking load of 50 kN has a working load of 10 kN. In the PPE sector, the factor is 10, meaning that a carabiner with a breaking load of 22 kN has a working load of 2.2 kN. The working load is computed as the breaking load divided by the safety factor; if the manufacturer has not specified a safety factor (e.g., in the instruction manual), a factor of 5 is utilized.