Crane and Power Line Entanglement: How to Stay Safe In the field of construction, safety comes first. Let us plunge into one vital lesson taught by Work Safe BC video on how to respond when a crane operator unintentionally makes contact with a high voltage power line: Safety Reminder: It is critical to ensure that safety is considered above all when dealing with heavy machinery near power lines. The film discusses an episode that emphasizes the need for vigilance and preparedness.
Danger Immediate? Shuffle Away: Your reaction matters when you find yourself in an unlucky situation where a crane connects with a high voltage power line. If you are in immediate danger, do not attempt to flee or get panicked but shuffle! Take small steps moving at least 10 metres away from the point of contact ensuring both feet remain touching the ground always. Do not Move if it’s Safe: When you are not in immediate danger, it is better to stay put until professionals arrive to help you out.
Smart Lifting: Unlocking Efficiency in Crane Industry
The world of lifting and cranes is going through a kind of revolution, powered by “Smart Lifting”, a new kind of technology. Just imagine cranes that can predict their own maintenance requirements and adjust their lifting paths to avoid obstacles in real time. They may even communicate with each other for operational optimization. Though it might sound fictional, it’s not taking long before the theory becomes practical.
So, what is Smart Lifting? It is the application of modern technologies like sensors, artificial intelligence, and big data into cranes and hoisting apparatuses. This includes:
Safety improvement: The sensors would identify potential risks thereby averting any accidents.
Enhanced efficiency: Real-time data analytics allows for optimizing lifting paths and reducing downtime.
Cost saving: Anticipatory maintenance makes equipment last longer and saves repair expenses.
More sustainable: Fuel consumption can be cut by smart systems as well as emissions reduced.
Smart Lifting’s implications can be felt in many aspects. It has the potential to make lifting safer and more efficient, as well as environmentally friendly. Data analysis and systems engineering are other employment opportunities that this technology will create.
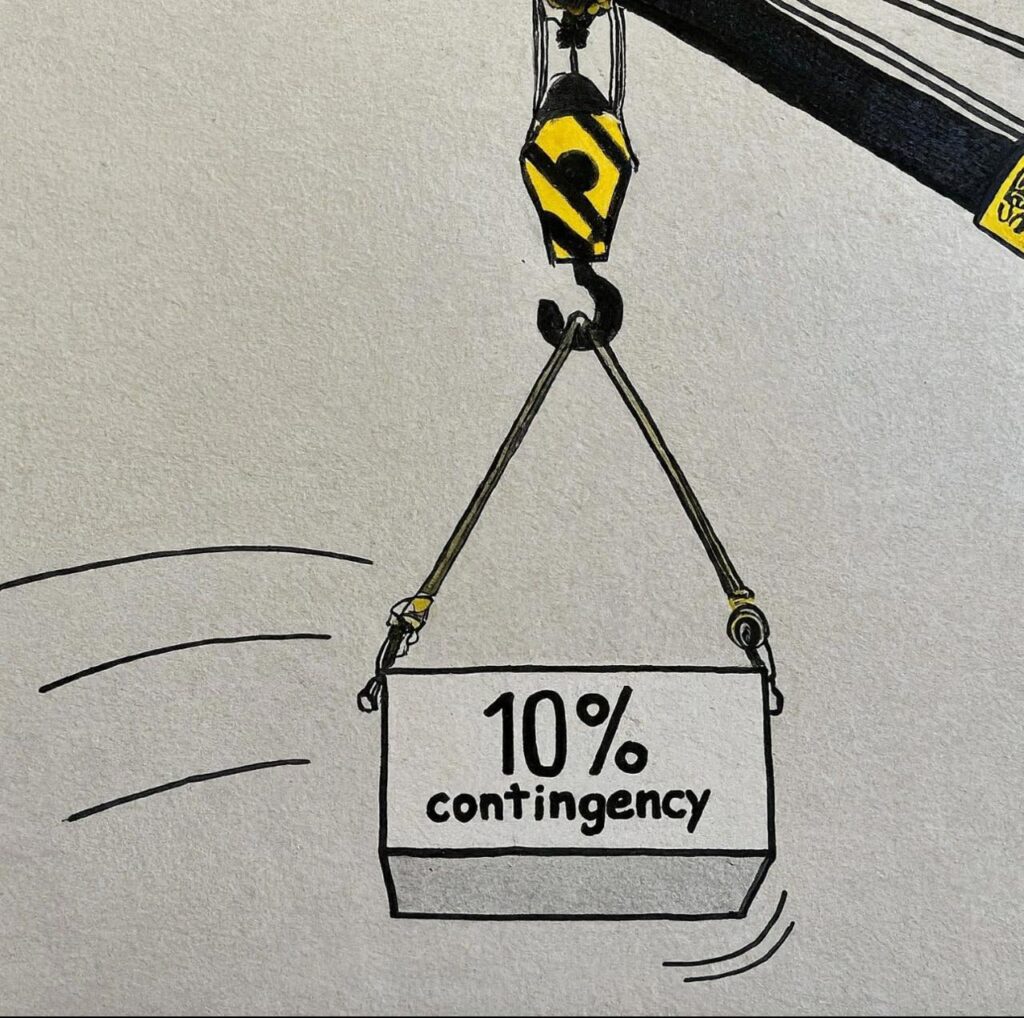
Contingency Factor: The Safety Net for Lifting Operations What is it? A weight margin added to the total load. Just like an extra layer of cushioning on the seat belt for those unexpected bumps on the road . Why is it important? Safety: Minimizes accidents and injuries. Compliance: Meets industry standards. Success: Increases the chance of a smooth lift. How much to use? Usually 10%, but more for risky lifts. Key factors: Inaccurate weight estimates Changing forces during the lift Weather conditions Equipment wear and tear Prioritizing safety with a contingency factor is not just a good idea, it’s essential for successful lifting operations Example Calculation: Let’s say you need to lift a load with an estimated weight of 500 kilograms. Contingency Factor: 10% Calculation: 500 kg 0.10 = 50 kg Total Load with Contingency: 500 kg + 50 kg = 550 kg Therefore, when planning the lift, you would need to select lifting equipment capable of safely handling a load of 550
How to examine a mobile crane before you use it properly!!!
- Perform a General Visual Inspection
Start by strolling round the crane. This involves observing whether there is anything that shows wear, tear or injury. In this case, you are required to search for elements with either screws missing or loose ones, cracks and dings. In addition to that, consider how clean the whole machine is. In fact, any excessive grease or dirt might be hiding more serious problems at hand. Furthermore, you can decide to have a checklist in your mobile crane safety inspection.
- Inspect The Hydraulic System
The hydraulic system acts as blood for the mobile crane. Therefore, check any signs of leakage, damage or wearing out of hydraulic lines and hoses. Also remember to ensure all connections are tight and hydraulics fluid hasn’t been contaminated by rusting residue inside them through corrosion.
- Inspect the Controls of the Crane
Lobotomize the crane control system. Check the switches, levers, and pedals for proper working conditions and smooth operation. Check the working of safety locks and emergency stop functions. Be sure to check all the warning labels and indicators.
- Examine the Lifting Mechanism of the Crane
Inspect wire ropes, sheaves, drums, blocks, and hooks for evidence of wear, twisting, kinking, or corrosion. Ensure the wire rope has the correct reeving with the functioning limit load indicators. The hooks should also be checked for deformation or cracks.
- Outrigger Inspection
It is usually the outriggers that give a crane its stability, so be sure to inspect their condition and verify that they extend and retract properly. Do not forget to check for bending and warping, nor for signs of damage, and confirm that the pads are clean and free of debris.
- Boom Inspection
The boom’s condition directly affects the crane’s ability to lift. Inspect the boom for any signs of damage, bending, or cracks. Check all the boom sections for proper alignment and ensure the telescoping mechanism is functioning correctly.
- Tire and Brake Condition
Satisfy yourself that the tire pressure, wear, and visible damage are up to standard. Also, check the state of the brakes by making sure they engage and release smoothly.
- Functional Tests
Conduct functional tests after properly performing the visual examination. Test the crane movements—for instance, hoisting, telescoping, and swinging—without any loads, which will help in checking correct operation.
- Operator Cab Inspection
Check for seatbelts, gauges, extinguisher, and all safety features ensure their good condition and operation. The cab should be cleaned with no loose objects; the operator must have a clear view.
Keep in mind that crane inspections are not only a requirement to be done before initial operation but also as a regular part of your overall safety program. If an inspection reveals a problem with the crane, the crane shall be removed from service until the problem has been corrected. A well-maintained crane is vital to having a safe and successful project.
SAFETY CHECKS BY LIFTING MACHINE OPERATOR BEFORE LIFTING OPERATION
- Everyday before starting to work the operator must carry out a safety check to ensure that everything is in order on the machine.
- Check the logbook on board the machine to verify that the periodical maintenance and instructions are well as all the necessary repairs have been carried out.
- Check boom lifting cylinder, auxiliary alarms and other safety devices are in working order
- Carefully inspect the load supporting parts like wire ropes, boom, outriggers and hooks
- Check for hydraulic oil and air leaks
- Before starting of the engine, check the cooling water and lubrication oil levels
- Once the engine is started, all the readings on the respective gauges are correct
- All controls check to be in working order
- No unauthorized field modification added counterweight and boom repaired improperly to check for any
- Checking of major hazards around the lifting zone relating to electricity, bad ground conditions, overload and wind speed monitoring before the lifting works started.
Critical Unsafe Act:
This act can lead to serious injury or can be fatal
Possible hazards:
- Crane toppling due to improper selection or overloading.
- Entrapment between outrigger and ground due to slipping or falling.
The Lifting operations can go wrong due to a variety of reasons, including:
Inadequate Planning: The poorly planned Lifting operations may result in accidents. This includes risk not assessed, no lifting plan, or no plan followed.
Wrong Equipment: The usage of incorrect types of lifting equipment or equipment that is not properly maintained, inspected, or certified can lead to failures.
Overloading: Overstraining the equipment beyond its lifting capacity can lead to mechanical failures and accidents.
Lack of Communication: Inadequate communication among the members of the lifting team is the cause of mistakes and accidents.
Insufficient Training: Inadequately trained operators and riggers in lifting operations and safety procedures are likely to make errors that can result in failures.
Environmental Factors: Adverse weather conditions like strong winds, rain, or poor visibility will impact the safety of the lifting operations.
Improper Rigging: If the rigging of the load is not correct or insecure, it may slip or fall while being lifted.
Human Error: This occurs when people make mistakes, such as miscalculations or disobeying procedures, because of poor judgment; hence, failure ensues during lifts.
Equipment Failure: Mechanical failure in lifting equipment, including cranes, hoists, or slings, arising from either wear and tear, defects, or an absence of maintenance measures.
Ground Conditions: Unstable or uneven ground conditions may cause the equipment to tip over or become unstable during the lift.
Control measures:
- The selection of appropriate cranes should be made in view of the actual weight of the lifting loads.
- The lifting capacity of the crane has to be higher than that of the load.
- Check whether the SLI and limit switch installed on the crane are functioning satisfactorily.
- Levelling of ground with suitable load-bearing capacity for the crane with the load must be ensured.
- The operator of the crane has to be competent and experienced.
- Barricade the space around the crane to deny access to unauthorized people.
- Cribbing plates to be placed under outriggers to improve stability further.
PRECAUTIONS IN OPERATION
- Calculation errors of the lifting capacity can lead to accidents
- The radius is the distance between the axis of rotation of the crane upper structure and the centre of the boom head sheaves
- Always stay within the normal capacity given in the table
- If the working surface is not capable of accepting load, then the crane will topple or swing
- Crane levels determine the working load capacity of a crane
CONTINGENCY STATEMENT OF LIFTING
- If there are any changes to any part of the lifting Plan then All operations will be halted
- Appointed person will consulted
- No further lifting is to take place until any changes made by appointed person in writing have been agreed and attached to the plans
- All personnel on the lifting plan have the proper authority to stop the lift if they believe it to be unsafe for any reason.
LIFTING SUPERVISOR RESPONSIBILITIES
- To ensure All lifting activities are executed as per the approval lifting plan
- Review the contents of LOP, JRA and MS completely
- Ensure the prestart briefings are take place before start lifting works
- Ensure that the signage, exclusion zone, e.t.c, are in place before the lifting takes place.
- Only third party-approved Riggers to give signals to the crane operator.
- All Lifting gear and accessories have valid, approved third-party certificates in place.
Taglines may also be tied at both ends sides for more control in high winds or if the load is a long one. Also, to keep a safe distances from the load it’s important to have a tagline long enough approx. 1.5 m times height of the load.
NOTE: Tagline shall be of natural fiber rope with a minimum diameter of 16mm.
Banks man or Rigger, You will be responsible not only for you own safety, but also for safety of others working in the vicinity of cranes, To ensure that a high level of safety is maintained.
Chain Calculation: Information given: Minimum Breaking Load of chain 40 Metric Tonnes Factor of Safety for chain = 4:1 We can calculate the Working Load Limit of the chain by using the formula: WLL=MBL÷FOS First convert the MBL from Metric Tonnes into kilograms. {1 Metric Tonne = 1000 kg} : MBL in kg= 40X1000=40000 kg Now, compute WLL: WLL=40000kg÷4=10000 kg So, the answer is the Working Load Limit of the chain, which is 10,000 kg. 2. Wire Rope Calculation Given information: Minimum Breaking Load of wire rope specimen=58.5 kN Factor of Safety for wire rope sling 5:1 Conversion 1 kg = 9.81 N We can calculate the Working Load Limit of the wire rope as follows : Convert the MBL from kN to kg MBL in kg =58.5*1000÷9.81 kg =5977.1 kg Now calculate WLL WLL=5977.1 kg÷5 =1195.42 kg
Question & Answer.
Q: What is a jib boom?
A: An extension attached to the main boom used when lifting light loads to a higher elevation than that permitted by the main boom.
Q: What is the purpose of a hoist limit switch?
A: To prevent over-travel of the hook block and the possibility of two-blocking.
Q: What is two-blocking? Why is
two-blocking dangerous?
Q: Two-blocking occurs when the hook block comes in contact with the upper sheave block during hoisting
of the hook (or lowering the boom), two-blocking is dangerous because that could cause damage of the crane, parting of the hoist lines and dropping the load.
DETERMINING THE WLL OF A FSWR( Flexible Sling Wire Rope) and Chain sling Each manufacturer shall provide a maximum WLL of a FSWR sling for lifting a load two ways;
- Fully Stamped in one end of the ferule or mechanically machine splice at the eye of the sling.
- On the information tag attached to one eye of the sling.
If this data is not available then the calculation ( Rule of Thumb) can be used
WLL=D×D×8
Take, for instance, if the FSWR sling measure 12mm in diameter. To find the WLL, one uses the formula below: WLL = D × D × 8 = 12 × 12 × 8
= 1152kg or 1.152t
For chain slings WLL of chain grade 80 or ‘T’ Grade chain the rule of thumb formula is
WLL=D×D×32
One link diameter is 12mm = 0. WLL =12×12×32 =4608kg or 4.608t
SLING ANGLES CALCULATIONS
Sling angles are used when two or more slings are used off a crane hook, and attached at different points on the load to be lifted.
-Maximum angle is 120° tension factor 1.0
-Recommended angle 90° tension factor 1.4
- Optimum angle is 60° tension factor 1.73
- Single wrap angel 45° tension factor 1.85
- Double wrap angel 60° tension factor 1.73
As the tension rises in the sling so the capacities are reduced.
Example -By 2t WLL sling by 60° angle
Max load= sling WLL × Angle factor
= 2 × 1.73 = 3.46ton - Now consider combination of angle factor Reeve factor and loads, Formula is
- Maximum load= Sling WLL × A/F × R/ F
- Example – Sling 8ton
- Angle 60°(1.73 A/F)
- Reeving around a square (0.5 Factor)
- WLL × A/F × R/F
- 8 × 1.73 × 0.5 = 6.92 ton
- Thus 6.92 ton is the maximum weight that can be lifted by 8 ton sling.
SLING TENSION CALCULATIONS
The most common case in the workplace is the selection of the proper lifting sling after establishing the weight of the load.
To determine the WLL of the sling required to lift a load divide the weight by angle Factor and by the Reeve factor
- Formula. WLL = Weight ÷ A/F ÷ R/F
Example – weight 20 ton
Angle 60°{A/F 1.73}
Reeved, a round load {0.75}
WLL = W ÷ A/F ÷ R/F
= 20 ÷ 1.73 ÷ 0.75
= 15.41 ton
Thus each sling shall have the capability to lift 15.41 ton.
OR you can use this formula below
Tension of Sling= sling length ÷ Height of slinging × Weight ÷ 2 or 3 according to the sling legs used to, Known as L ÷ H × W ÷ 2 or 3= T (sling tension). These are sling selecting scenarios.
CALCULATIONS FOR LOAD FACTOR
A rigger and operator must know the load factors for each method of slinging in order for them to sling loads properly.
The load factor is the WLL reduction of a Sling when it is reeved around or connected to a load.
REEVING. FACTORS
- Connected direct and straight on load= 1
- Basket hitch on a square load. =1
- Basket hitch on a round load. =2
- Choker hitch on a round or square. =0.75
- Rectangular load. =0.50
- Direct load ( example WLL of sling is 1ton)
Max load= factor ×WLL
Max load= 1×1=1t - Rectangular load
Max load= factor × WLL
= 0.5×1=0.5t
*Round load choke hitch
Max load= factor × WLL
=0.75 x 1 =0.75t - Basket hitch
Max load= factor ×WLL
=2 × 1=2t
NB. This is maximum load that can be lifted with this sling of 1ton.