There you have it Safely maintenance.
What is maintenance safety?
Maintenance safety should be a top priority for the maintenance and operations teams. Whenever your maintenance crew works on a piece of equipment, they must follow proper safety procedures. In addition to preventing major injuries, doing this can help your facility continue to run smoothly.
Maintenance safety not only involves safety protocols for those performing repairs, but it also includes regular checks to make sure safety equipment is functioning properly.
Why businesses use maintenance safety precautions:
There are many reasons why businesses use maintenance safety precautions, most of which are highly practical.
Keep workers safe.
First and foremost, the purpose of maintenance safety precautions is to keep workers safe. Maintenance workers reduce their risk of injury by adhering to the correct practices.
Protect machinery:
Maintenance safety procedures also protect equipment. For instance, a proper lockout-tagout (LOTO) procedure makes sure machines don’t randomly start up during repairs. If certain protocols are not followed, an arbitrary equipment startup could harm the machinery as well as adjacent workers.
Routine safety checks also help maintenance teams keep machinery in top working condition, minimizing breakdown time and prolonging equipment life.
Produce on time.
Safety issues not only cause injuries but also delays. If a piece of equipment breaks down and causes an injury, that can significantly delay production.
In order to keep to your production timelines, you need to make sure your equipment is operating at safe levels. Anything less puts production losses and unscheduled downtime at risk.
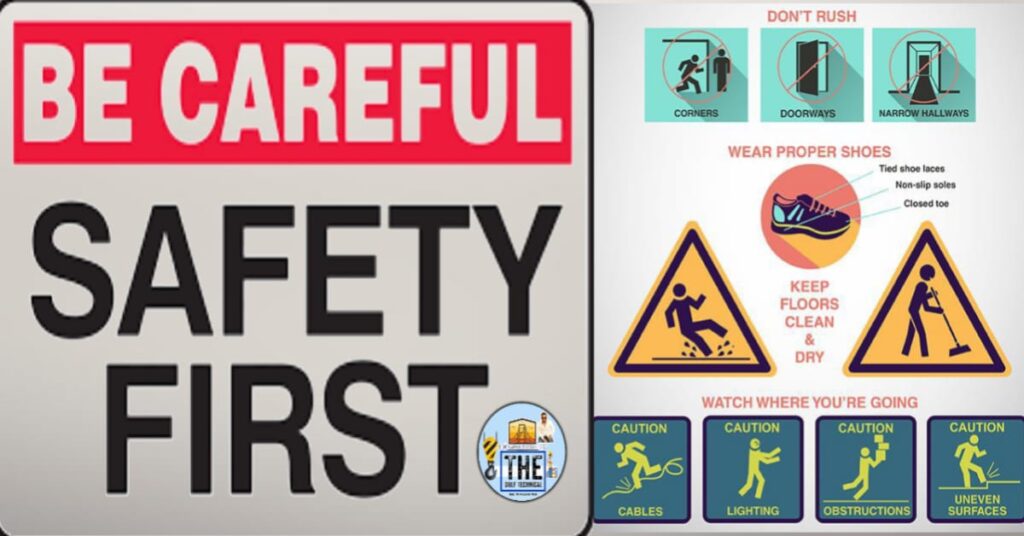
Maintain peace of mind for workers.
Employees feel safer, and there is less chance of injury when there are enough safety measures in place. When your operations and maintenance crews come in knowing that the machinery they’re working on is safe to use, they’re able to work with less fear and more efficiency. Ultimately, more gets done faster.
Also read more: Daily Safety Precautions
The best practices for promoting maintenance safety are:
There are best practices to adhere to while safeguarding your staff and equipment. Six of these are detailed below.
Stick to a schedule.
First off, keep to a regular safety check schedule. Safety checks on machinery, maintenance tools, and personal protective equipment (PPE) should all be handled on a routine basis.
Use authorization keys:
Hazardous pieces of equipment should be restricted with specific authorization. In this manner, you can restrict access to people who have received enough training.
There is less chance that someone may start an item of equipment while a technician is working on it if only a select few people know the code.
Fran Candelera
Fran Candelera Nice post. I learn something totally new and challenging on websites
Blue Techker
Blue Techker You’re so awesome! I don’t believe I have read a single thing like that before. So great to find someone with some original thoughts on this topic. Really.. thank you for starting this up. This website is something that is needed on the internet, someone with a little originality!
FinTech ZoomUs
FinTech ZoomUs I just like the helpful information you provide in your articles
موازين الشحن العراق
BWER leads the way in weighbridge technology in Iraq, delivering customized weighing solutions that are accurate, efficient, and ideal for heavy-duty use in any environment.
noodlemagazi
Noodlemagazine There is definately a lot to find out about this subject. I like all the points you made
Registrácia na binance
Thank you for your sharing. I am worried that I lack creative ideas. It is your article that makes me full of hope. Thank you. But, I have a question, can you help me?
hentairead
hentairead For the reason that the admin of this site is working, no uncertainty very quickly it will be renowned, due to its quality contents.