๐๐ป๐๐ฟ๐ผ๐ฑ๐๐ฐ๐๐ถ๐ผ๐ป:
Visual inspection is an essential part of valve maintenance and can help identify potential issues or damage during valve inspection that may affect the valve’s performance.
๐๐
๐๐ฒ๐ฟ๐ป๐ฎ๐น ๐๐ป๐๐ฝ๐ฒ๐ฐ๐๐ถ๐ผ๐ป:
Examine the external components of the valve, including the body, bonnet, stem, handwheel, and any other visible parts. Look for signs of corrosion, leaks, cracks, or any other visible damage. Check for loose or missing bolts, gaskets, or seals.
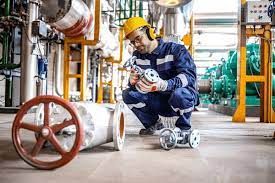
๐ฉ๐ฎ๐น๐๐ฒ ๐ข๐ฝ๐ฒ๐ฟ๐ฎ๐๐ถ๐ผ๐ป:
Operate the valve through its full range of motion to ensure smooth operation. Observe the valve’s movement and listen for any unusual sounds, such as grinding, scraping, or excessive noise.
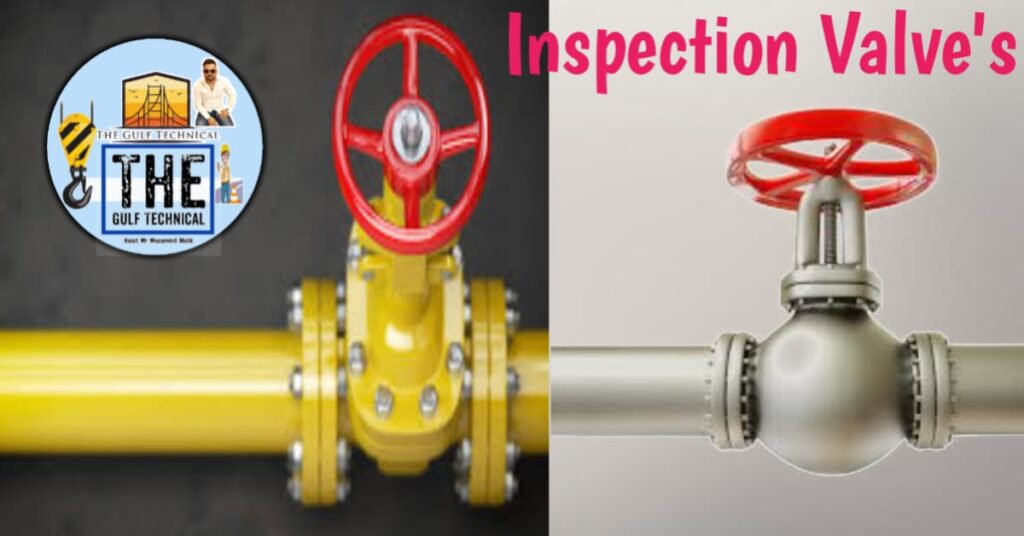
Valve Inspection Checklist:
Valve evaluation is typically conducted on-site at the factory before shipment, and it’s especially popular for first-time purchases from valve suppliers in India or China.
Inspectors will assess the equipment based on various criteria, using ISO 2859 sample plans or G2 inspection sample plans to determine sample size and acceptance criteria for quality inspection of valves. This process is carried out before the valves are shipped, ensuring a thorough evaluation of their quality.
๐ฆ๐๐ฒ๐บ ๐ฎ๐ป๐ฑ ๐ฃ๐ฎ๐ฐ๐ธ๐ถ๐ป๐ด:
Inspect the valve stem for signs of bending, corrosion, or excessive wear. Check the stem packing for leaks or damage. If the valve has a gland nut, ensure that it is properly tightened but not overly tightened.
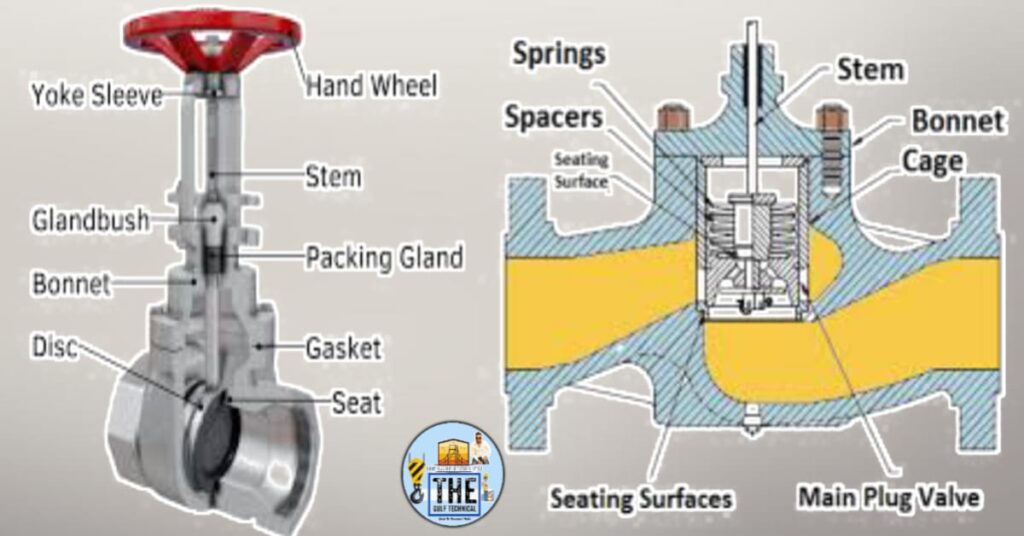
๐ฆ๐ฒ๐ฎ๐ ๐ฎ๐ป๐ฑ ๐๐ถ๐๐ฐ:
Inspect the valve seat and disc for signs of damage, wear, or pitting. Look for any foreign objects that may be lodged between the seat and disc. Ensure that the disc moves freely and seats properly when closed.
๐๐ผ๐ป๐ป๐ฒ๐ฐ๐๐ถ๐ผ๐ป๐:
Check the valve connections, such as flanges or threaded connections, for leaks, damage, or signs of loosening. Tighten any loose connections as necessary.
Mahtab
Good
ะฒะดะบัะธัะธ ะฐะบะฐัะฝั ะฝะฐ ะฑะฝะฐะฝั
Thanks for sharing. I read many of your blog posts, cool, your blog is very good.
Prijava za prejem 100 USDT
I don’t think the title of your article matches the content lol. Just kidding, mainly because I had some doubts after reading the article.
Create Personal Account
Your point of view caught my eye and was very interesting. Thanks. I have a question for you.
cรณdigo binance
I don’t think the title of your article matches the content lol. Just kidding, mainly because I had some doubts after reading the article.
Sign Up
Thanks for sharing. I read many of your blog posts, cool, your blog is very good.
Iscriviti a binance
Thank you for your sharing. I am worried that I lack creative ideas. It is your article that makes me full of hope. Thank you. But, I have a question, can you help me?