Assurance of the Effectiveness of Pressure Safety Valves (PSVs) in Hazard and Operability Studies (HAZOP)
Pressure safety valves (PSVs) are pivotal guardians against overpressure events, preserving the integrity of equipment in industrial processes. However, when integrating them into a Hazop study, meticulous consideration of various factors is essential to guaranteeing their efficacy.
Key Considerations:
1) Set Point Precision:
Set points must be meticulously calibrated, ensuring they are sufficiently low to safeguard the designated equipment effectively.
2) Sizing for Varied Scenarios:
PSVs should be sized for the governing blocked flow overpressure case, but versatility in sizing for scenarios like thermal fire, reverse flow, or valve failure is also prudent.
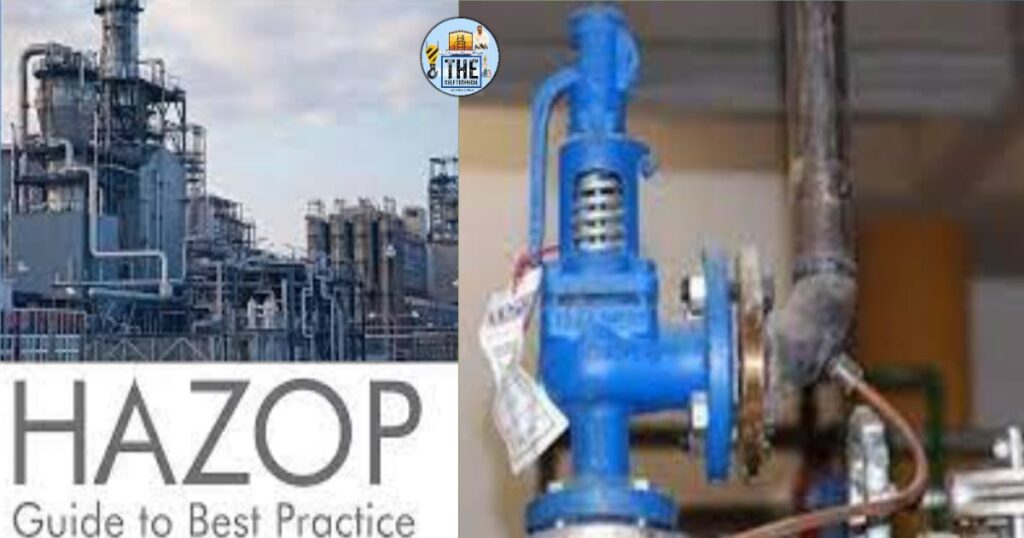
3) Strategic Relief Location:
Relief paths must lead to safe locations such as flares, steering clear of atmospheric venting to mitigate the risks of fire, explosion, or exposure to hazardous gases.
4) Unobstructed Flow Paths:
It is crucial to have an unimpeded and uncluttered flow path to the relief point in order to prevent any blockages from compromising the PSV’s efficiency.
5) Back Pressure Vigilance:
Preventing back pressure is critical; it ensures that PSVs can lift at the required set point, maintaining their ability to counteract overpressure.
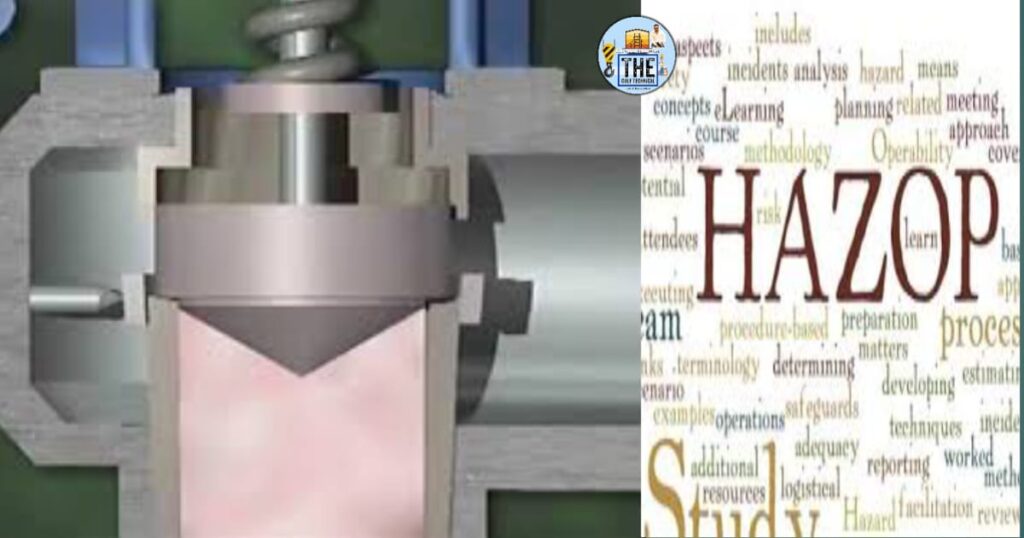
6) Service-Specific Reliability:
Consider the type of service when assessing reliability; 99% reliability is typical for clean service, with no credit given for dirty service due to potential plugging.
7) Mitigating Common Cause Failure:
When evaluating PSVs subjected to comparable process circumstances, care should be taken, and a 90% reliability factor should be applied to account for any common-cause failures.
8) Joule-Thompson (JT) Effect Awareness:
Vigilance against the JT effect across PSVs is crucial, as a significant temperature drop could lead to piping integrity issues.
9) Discharge Piping Design:
Proper design of discharge piping is imperative, not only for the functionality of PSVs but also for the safety of operators, reducing the risk of overpressure events.
In HAZOP studies, attention to these factors ensures that PSVs play their vital role effectively, contributing to a safer and more reliable industrial environment.
Also Read More, Inspection Test Plan Methods Checklist: QA/QC
The Inspection and Test Plan( ITP) is an inspection checklist that includes those characteristics that should be checked at each stage of the process. It might encompass every facet of your workflow.
In QA/QC, an inspection test plan (ITP) usually consists of the following components:
1) Project information:
- Project name, location, and reference documents.
2) Scope:
- Clearly defined boundaries specify what is covered by the inspection.
3) Objectives:
- Specific goals and outcomes of the inspection.
4) Reference Standards:
- Applicable industry codes, standards, and specifications.
5) Responsibilities:
- Roles and responsibilities of individuals involved in the inspection.
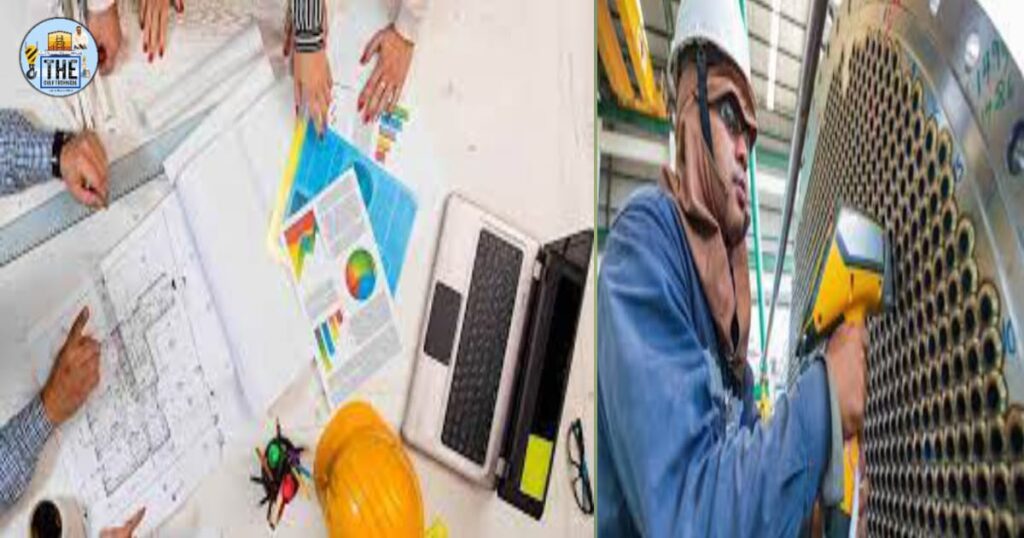
6) Inspection Criteria:
- Detailed criteria for evaluating the quality of the work or product.
7) Inspection Methods:
- Procedures and techniques were used during the inspection.
8) Sampling Plan:
- information on the procedure and timing of sample collection for inspection.
9) Documentation and Records:
- Requirements for recording and maintaining inspection data.
10) Acceptance Criteria:
- a set of precise requirements that specify whether the job or product satisfies accepted standards.
11) Non-Conformance Handling:
- Procedures for dealing with identified non-conformities or deviations.
12) Schedule:
- Timelines and milestones for the inspection process.
13) Communication Plan:
- How information will be communicated among stakeholders.
14) Approval Process:
- procedures and requirements for receiving permission following a successful inspection.
15) Review and Revision:
- Mechanism for periodic review and revision of the inspection test plan.
16) Training Requirements:
- Any specific training is needed for personnel involved in the inspection.
17) Safety Considerations:
- Safety measures and precautions during the inspection.
18) Documentation and Reporting:
- Procedures for documenting and reporting inspection results.
Recall that these are standard elements of an inspection test plan found in the context of quality assurance and control; the specifics may differ depending on the project or industry.
Tech to Force You’re so awesome! I don’t believe I have read a single thing like that before. So great to find someone with some original thoughts on this topic. Really.. thank you for starting this up. This website is something that is needed on the internet, someone with a little originality!